Not Tata Motors Nano, Tiago and Tigor are powering Sanand
Tata Motors is looking at a 30% rise in production from its Sanand plant in Gujarat, which is nearing saturation at 1.3-1.4 lakh units per annum. The move is a part of increasing operational efficiency at the facility, said Mayank Pareek, president of the passenger vehicles business unit.
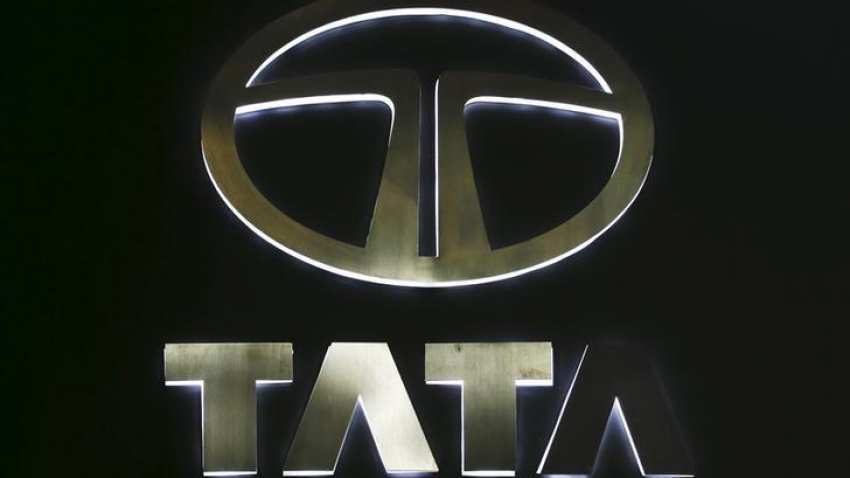
Tata Motors is looking at a 30% rise in production from its Sanand plant in Gujarat, which is nearing saturation at 1.3-1.4 lakh units per annum. The move is a part of increasing operational efficiency at the facility, said Mayank Pareek, president of the passenger vehicles business unit.
Sanand had an installed capacity to make 2.5 lakh Nano cars per annum. However, with Tiago and Tigor being produced here, the capacity has reduced to 1.3-1.4 lakh units a year.
The company, which reported a loss of Rs 1,902 crore during the first quarter ended June 30, is on an efficiency enhancement drive to increase production with near zero capital investment. This fiscal, it aims to improve efficiency six times more than it had done in past, and next year, it would again double it.
The Sanand facility is critical for Tata Motors as it delivers about 60% of passenger vehicles for the company, manufacturing close to 8,000 Tiago cars, 3,500 units of Tigor and Nano cars as per demand.
In sales and service as well, Tata Motors is betting high on digital showrooms and a mobile app to accelerate expansion at lower cost and serve consumers better. “For long we have been playing a chasing game. Now is the time to set rules,” Pareek told media persons at the company’s Sanand plant.
Relying on a healthy mix of digital technologies and traditional brick-and-mortar showrooms, the company plans to increase its sales network from 787 outlets to 850 by the end of the year and take it close to 2,000 in the next four years. It is adding close to 200 locations every year and plans to launch a mobile app that could make the supply of spares to service centres more efficient.
The company is also looking to make Sanand a major hub to manufacture electric vehicles (EV). However, the cost of batteries and availability of charging infrastructure are key bottlenecks, feels Pareek.
Source: DNA MoneyNot Tata Motors Nano, Tiago and Tigor are powering Sanand
Tata Motors is looking at a 30% rise in production from its Sanand plant in Gujarat, which is nearing saturation at 1.3-1.4 lakh units per annum. The move is a part of increasing operational efficiency at the facility, said Mayank Pareek, president of the passenger vehicles business unit.
Sanand had an installed capacity to make 2.5 lakh Nano cars per annum. However, with Tiago and Tigor being produced here, the capacity has reduced to 1.3-1.4 lakh units a year.
The company, which reported a loss of Rs 1,902 crore during the first quarter ended June 30, is on an efficiency enhancement drive to increase production with near zero capital investment. This fiscal, it aims to improve efficiency six times more than it had done in past, and next year, it would again double it.
Watch this Zee Business video here:
The Sanand facility is critical for Tata Motors as it delivers about 60% of passenger vehicles for the company, manufacturing close to 8,000 Tiago cars, 3,500 units of Tigor and Nano cars as per demand.
In sales and service as well, Tata Motors is betting high on digital showrooms and a mobile app to accelerate expansion at lower cost and serve consumers better. “For long we have been playing a chasing game. Now is the time to set rules,” Pareek told media persons at the company’s Sanand plant.
Relying on a healthy mix of digital technologies and traditional brick-and-mortar showrooms, the company plans to increase its sales network from 787 outlets to 850 by the end of the year and take it close to 2,000 in the next four years. It is adding close to 200 locations every year and plans to launch a mobile app that could make the supply of spares to service centres more efficient.
The company is also looking to make Sanand a major hub to manufacture electric vehicles (EV). However, the cost of batteries and availability of charging infrastructure are key bottlenecks, feels Pareek.
Source: DNA Money
09:45 AM IST